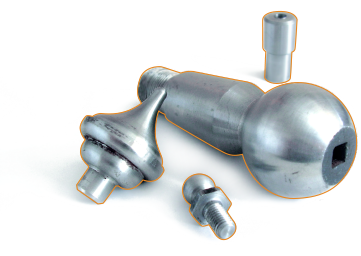
Про компанію
Приватне підприємство “Родон” засноване в 1995 р. в м. Львові.
Основна спеціалізація: виконання токарних робіт з використанням високопродуктивного обладнання з числовим програмним керуванням та одно і багатошпіндельних токарних автоматів.
Основний потенціал нашого підприємства – це індивідуальний підхід до вирішення питань кожного клієнта, професійне виконання замовлення, використання передових технологій і сучасного інструменту у виробництві.
Виробничі задачі, які ми вирішуємо: токарна, фрезерна та слюсарна обробка металу (виготовлення деталей типу корпусів, втулок, дисків, кілець, фланців, кронштейнів, валів, осей, роликів, гайок, болтів… із кольорових і чорних металів, пластмаси та інших матеріалів). Виконується обробка циліндричних, конічних, фасонних і торцевих поверхонь, нарізка різноманітних внутрішніх та зовнішніх різьб: метричних, трубних, конічних, багатозахідних, модульних, торцевих, а також накатка різьб; свердління і розвертання отворів і т.д.
Механічну обробку здійснюємо, користуючись як вітчизняним, так і інструментом провідних світових виробників: ISCAR, SANDVIK, Taegu Tec, Seco…
Наші контакти
Тел./факс: 032 275 59 29